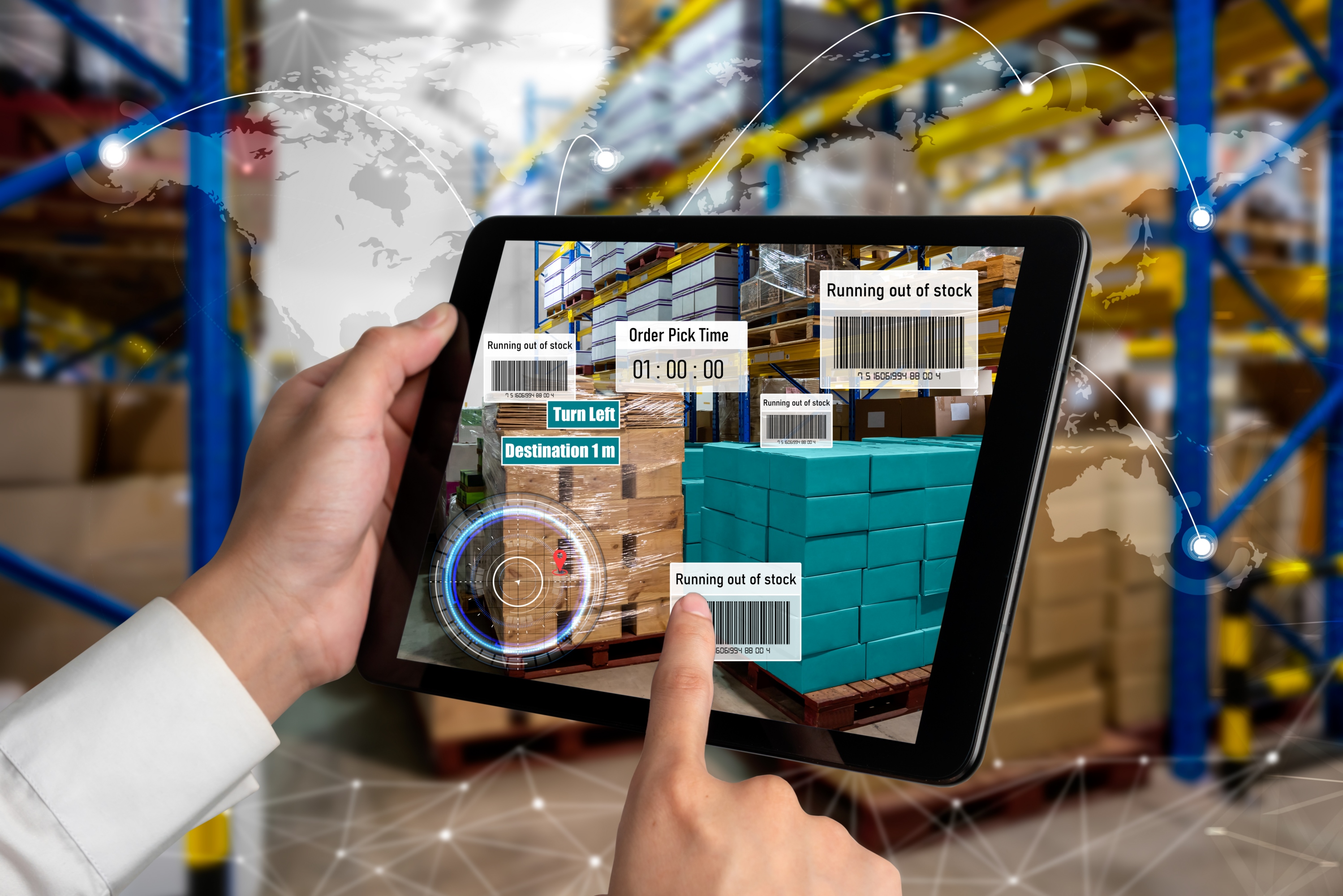
Top 10 Essential Functional Requirements for Warehouse Management Systems
What is Warehouse Management?
Before we can get into a complex topic such as warehouse management system functional requirements, we should first define the subject. Indeed, warehouse management is one of the latest supply chain technology trends.
The term refers to the process of performing, monitoring, and improving various warehouse operations. This includes overseeing and optimizing any activities a warehouse needs to complete. A few examples include:
Order fulfillment
Stock management
Storage optimization
Return Management
Reporting and analytics
Though warehouse management is a process, the term is typically used to refer to the software systems designed to aid in warehouse management functions. These warehouse management systems, or WMS, can use any number of performance metrics and real-time data analysis to help warehouse managers reduce costs, improve order accuracy, and save time.
But what exactly are these warehouse management functions? Moreover, what are some warehouse management system requirements that everyone in the logistics industry should know? As supply chain management software requirements change and grow, staying informed is key.
Essential Functions of Warehouse Management
Warehouse management systems are one of many supply chain development services helping to automate global logistics. Because they can eliminate much of the guesswork and human error involved in warehouse business processes, they can drastically improve virtually any operation. Though there are many different warehouse-receiving software types, including custom-designed models, the industry has a few standard WMS requirements.
Examples of Warehouse Management System functional requirements:
Reduce Risks
A WMS system can help reduce risks by minimizing errors and improving accuracy throughout the inventory control and management process. It does this by ensuring that products are properly received, stored, and shipped, reducing the chances of misplacements, incorrect shipments, or lost inventory. Most of these systems provide real-time inventory visibility, help automate processes, and identify potential logistics risks before they become a problem.
Goods Movement
The ability to move goods is the basis for the entire logistics industry. Therefore, doing so efficiently while seeking to lower shipping costs is one of the primary warehouse management functions. A good WMS will aid in goods movement by optimizing workflows, providing clear instructions during pick and pack, and directing employees to the right locations within the warehouse. The system can also track the movement of goods in real-time, enabling supervisors to monitor progress and make changes on the fly, if necessary.
Storage Space
Efficient utilization of storage space is essential to maximize warehouse capacity and minimize costs. A WMS helps achieve this by optimizing inventory placement and considering factors such as item characteristics, demand patterns, storage requirements, and warehouse layout. Many systems are capable of suggesting improved storage locations, determining optimal picking paths, and preventing both overcrowding and underutilization of space.
Ensuring Stable Prices
Of all the warehouse management system requirements, contributing to price stability is crucial for maintaining accurate, up-to-the-minute inventory information. Through real-time tracking is helpful enough, a WMS can analyze vast amounts of internal and external data to provide insights into demand patterns and generate forecasts. A business can then use this demand forecasting information to avoid stockouts and overstock situations, which can lead to price fluctuations.
Value Added Services
There are loads of microservices in supply chain software nowadays. Depending on the design of the WMS, it may be able to offer value-added services that go beyond basic warehouse automation. Examples include:
Order customization
Kitting (combining individual products into sets)
Bundling (combining multiple products into a package deal)
Labeling
Warehouse safety analysis
Value-added services also allow businesses to differentiate themselves from competitors, attract more customers, and create additional revenue streams. In the end, it’s important to consider the function of the warehouse management system early and reevaluate it often.
Crucial Warehouse Management System Features & Requirements
Beyond the essential functions listed above, there are a number of warehouse management requirements to consider when buying or building a WMS. Though many businesses in the supply chain management space have similar requirements, many also have unique needs that set them apart from the pack.
Of course, you don’t need to know how to implement a supply chain management system on your own to understand basic warehouse management requirements. Below is a list of common warehouse management software features you and your team will want to consider.
Inventory Management
Example of inventory management system Inventory management is everything to a warehouse manager. Though nearly every warehouse management system functions in this way, the results are not created equal. Some of the things you should look for in a good inventory management WMS are overall visibility, forecasting functions, purchasing history analysis, and in-warehouse tracking capabilities. If you work in perishable goods, having a WMS that can track movement based on dates and times might also be essential.
Inventory management system requirements to look for:
Cross Docking
Barcode Scanning
Cycle Counting
Physical Inventory Count
Reordering
De-kitting
Digitization
The average warehouse office used to be a nightmare of papers, charts, and maps. Today, smart warehouse managers know that technology is the biggest component of any successful operation. So, if you’re attempting to digitize your warehouse, your WMS should be able to integrate with ERP systems already in use (or those you plan to implement). When shopping WMS, make sure you determine whether it will “play well” with the others.
Receiving and Storage Operations
A good warehouse management system should support numerous shipping and receiving functions. Examples include generating receipts, managing holds, verifying and inspecting incoming items, and more. After all, shipping and delivery are not some rudimentary processes. There are thousands of moving parts to be considered at every step in the process. The more parts your new WMS can handle, the further you can streamline your operation.
Specific features to look for:
(RFID) Interface
SKU generation (manual or otherwise)
Data based receiving and putaway
ASN receiving
Order Management and Picking
Example of order management system
Order picking refers to the process of retrieving and assembling the items or products from their storage locations. It is not only time-consuming but takes up a huge amount of any warehouse’s operating costs. Of course, order picking and the processes supporting it are crucial to order fulfillment. However, that doesn’t mean they can’t be handled by a well-designed WMS. Many warehouse managers prioritize this feature due to its ability to reduce costs, improve customer satisfaction, and dramatically increase order accuracy.
Specific features to look for:
Partial Picking
Directed Voice Picking
Vision Picking
Wave Picking
Batch and Cluster Picking
Zone Picking
Shipping and Logistics
Shipping is a fundamental aspect of warehouse management, and is, therefore, a crucial feature for any WMS. In many cases, these systems will also incorporate separate Transportation Management Systems (TMS), which are capable of optimizing shipments, handling planning, and optimizing execution to enhance the overall efficiency of shipping efforts. Again, not all WMS designs do this in the same way. One might support multiple modes, such as multimodal and intermodal, while others can only concentrate on a single mode of transportation. Though it’s possible to have a separate TMS, it’s still essential that it integrate with your WMS, as this is integral to achieving real-time visibility and maximizing customer satisfaction.
Specific features to look for:
Freight Procurement
Cold Chain Management
Picking and Put away
Goods Check-in
Packing and Dispatch
Digital Assistants
Goods Arrival
Fleet Monitoring
Labor Management
Example of labor management system
Again, digitization aims to improve and optimize as many warehouse processes as possible. So aside from the features that identify, monitor, and organize material handling, many WMS designs will also feature warehouse labor management systems. After all, effective labor management can go a long way toward keeping employees on task and helping identify areas where human resources aren’t being properly utilized. Every system works a bit differently, but they typically include some way to track hours, analyze PTO, and match individual staff members to specific tasks or orders.
Specific features to look for:
Labor Planning
Scheduling
Employee Engagement
Warehouse Safety Management
Labor Allocation
Labor Cost Optimization
Cartonization
In the context of warehouse management, cartonization refers to the process of determining the optimal placement of items within shipping cartons or containers. To do this properly involves analyzing the dimensions, weight, and quantity of individual items, and then calculating the most efficient arrangement to maximize the utilization of the available carton space. Immediately, this is a must-have feature for any warehouse that ships a wide variety of products. A WMS will typically utilize algorithms to select items and determine how to pack them as efficiently as possible. Over time, this can contribute to significant shipping cost savings while also reducing worker hours.
Specific features to look for:
Single Level Cartonization
Multi-level Cartonization
Container Loading
Container Splitting
Container Management
Life Cycle Tracking
Life cycle tracking refers to the monitoring and management of a product's life cycle within the warehouse, from its arrival to its eventual disposal or return. Any warehouse manager will tell you that it’s an essential part of their job because it helps ensure that inventory levels are as accurate as possible. In turn, this provides valuable insight into how inventory is being utilized. A good WMS solution will include ways to generate accurate records of each product’s journey through the warehouse, allowing managers to identify potential problems wherever they might occur. These systems can also be programmed to track based on things like lot numbers, serial numbers, and both expiration and manufacturing dates.
Integration with Existing Software
The term enterprise resource planning (ERP) refers to any software system designed to help you run your business, regardless of the industry in which you operate. ERPs support automation at many different levels and can include any number of sub-systems. Whether you have such a system in place or merely plan to implement one, it’s essential that the WMS you purchase or build be able to integrate. This integration is what enables seamless data flow, enhances efficiency, provides real-time visibility, automates processes, supports scalability, and enables comprehensive reporting and analytics.
Enhance Your Warehouse Management: Practical Tips
Warehouse managers are always looking for ways to enhance and streamline their operations – at least, they should be. From stock replenishment to vendor management, the scalability and flexibility of warehouse processes are something that can always be improved upon. To that point, here are a few practical tips to help you improve your overall approach to warehouse management.
Make Safety a Top Priority
The most efficient warehouses are also the safest ones. Having rigorous safety standards can not only protect your most valuable assets (your workers), but help you avoid accidents and hazards that cost both time and money. Make sure that safety measures are in place and followed rigorously within the warehouse. This includes providing appropriate safety equipment, conducting regular safety training sessions, and promoting a safety-conscious culture among employees. You should also implement facility-specific protocols and regularly inspect the warehouse to identify and address potential hazards.
Improve Organization Process
The efficient organization is crucial for smooth warehouse operations. Ignoring how your facility is organized can cost you a fortune over time. Start by optimizing the layout of the warehouse to minimize travel time and maximize storage capacity. Use clear labeling and signage to make it easy for employees to locate items quickly during pick and pack. Also, make sure to implement some sort of systematic inventory management system so that you can track inventory levels accurately, reduce errors, and ensure efficient order fulfillment. Try to remember that every step to your workers has a cost associated with it. If your staff is running around the warehouse all day in a disorganized fashion, you're leaving significant funds on the table.
Avoid Manual Data Entry
As previously mentioned, most warehouses have long since moved on from anything we might recognize as “manual data processing.” Manual data entry is time-consuming and prone to errors due to the amount of human involvement in the process. Consider implementing technologies to eliminate or minimize manual data entry tasks to avoid these costly hangups. Barcode scanners, RFID technology, and automation software can help capture and process data accurately and efficiently. This can drastically reduce the occurrence of errors while also improving overall productivity. This is especially true for any task that involves calculations, which can cause catastrophic failures due to even minor mistakes.
Train Employees
Employee training and workplace safety go hand in hand. That’s why it’s so important to invest in regular training programs to enhance the skills and knowledge of warehouse employees. Make sure you provide thorough training on the proper handling of equipment, safety procedures, inventory management techniques, and the use of warehouse management systems. Also, make sure to update the training when necessary. Remember, well-trained employees are not only more efficient, but they’re also better equipped to handle their responsibilities.
Integrate a Warehouse Control System (WCS)
Given the rest of this article, it should come as no surprise that one of our biggest practical tips for enhancing warehouse management is to implement a Warehouse Control System. After all, these useful software solutions are indispensable in helping to streamline and automate various warehouse processes, from order picking and inventory replenishment to shipping. By optimizing the flow of goods and reducing errors, you can significantly improve the way your operation functions while simultaneously cutting costs.
Having a User-Friendly Interface
If investing in a WMS, select one with a user-friendly interface. The system should be intuitive and easy to navigate, requiring minimal employee training to use effectively. A user-friendly interface simplifies tasks, reduces the chances of errors, and increases employee productivity while avoiding the need for constant tech support and updates to training. Remember, the goal is to use your WMS to save time, not waste time learning how to use your WMS!
Building Scalability and Flexibility for Future Technologies
Of all the warehouse management system functional requirements we’ve discussed, preparing for future growth and technological advancements is among the most vital to your overall warehouse management strategy. For example, look for scalable solutions that can adapt to increasing inventory volumes, changing business needs, and evolving industry trends. Stay updated with emerging technologies, such as robotics, artificial intelligence, and predictive analytics, as they may have the ability to enhance your efforts even further.
How Inventorsoft Can Help You with Warehouse Management
At Inventorsoft, we have nearly a decade of experience providing state-of-the-art supply chain management software solutions. These include designing highly effective inventory management systems. If you’re considering a WMS, contact Inventorsoft today. Our results-focused team will be more than happy to discuss how we can help you create a solution that meets all the stipulations discussed in this article and so much more.
Whatever your warehouse management requirements, Inventorsoft can help.
Related articles
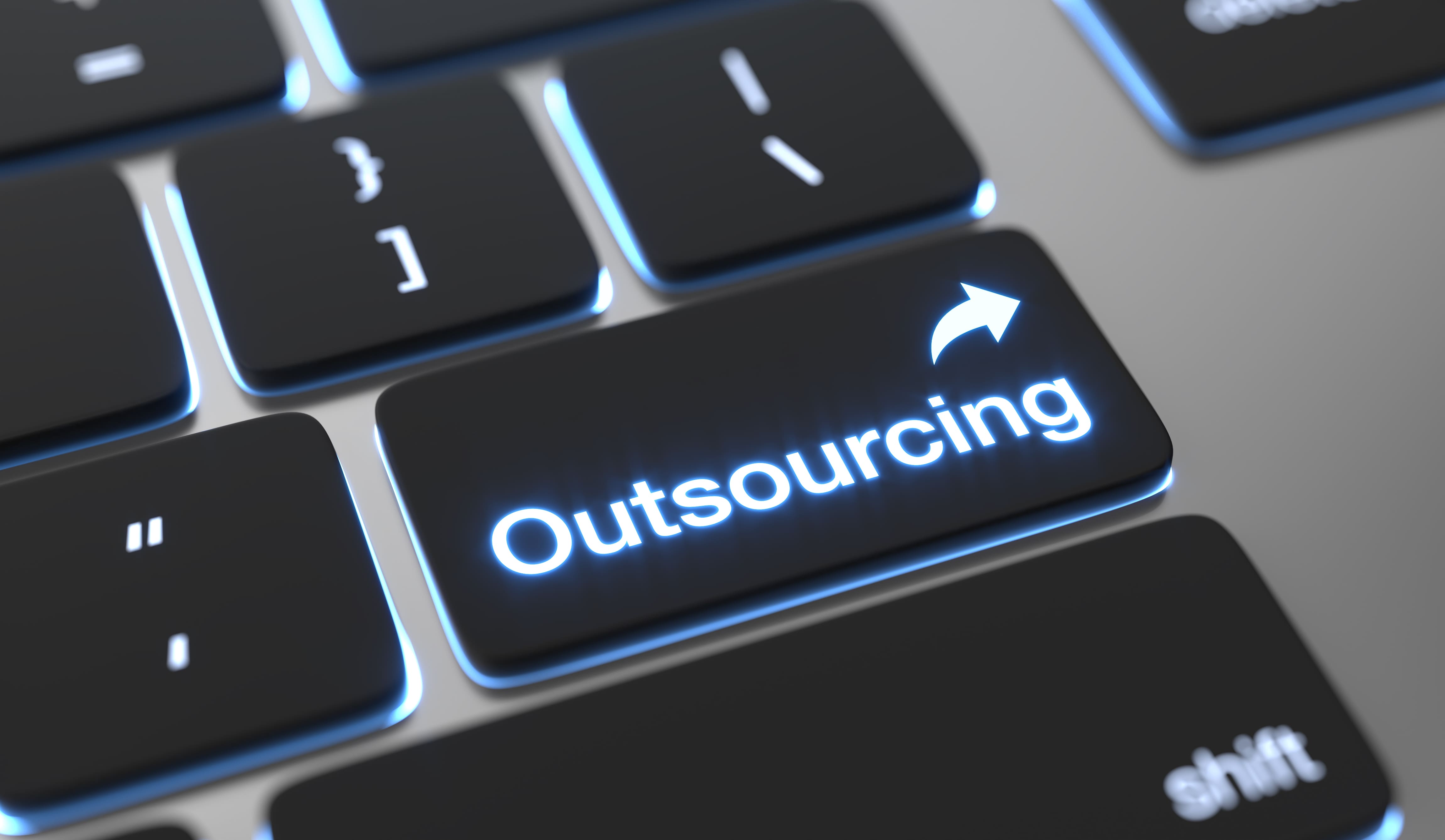
Outsourcing vs Outstaffing: What’s the Difference and Which Should You Choose?
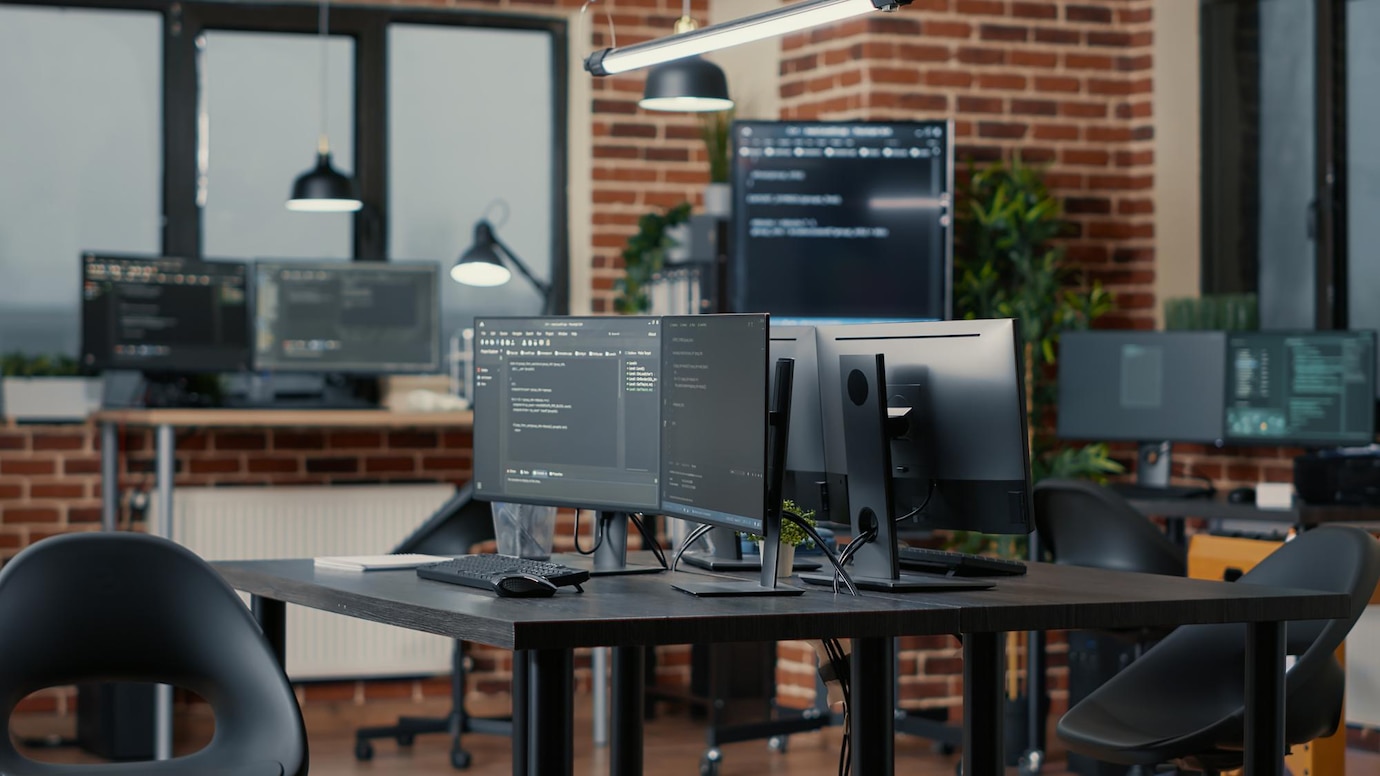
The Discovery Phase of a Software Development Project: What It Is and Why You Need It
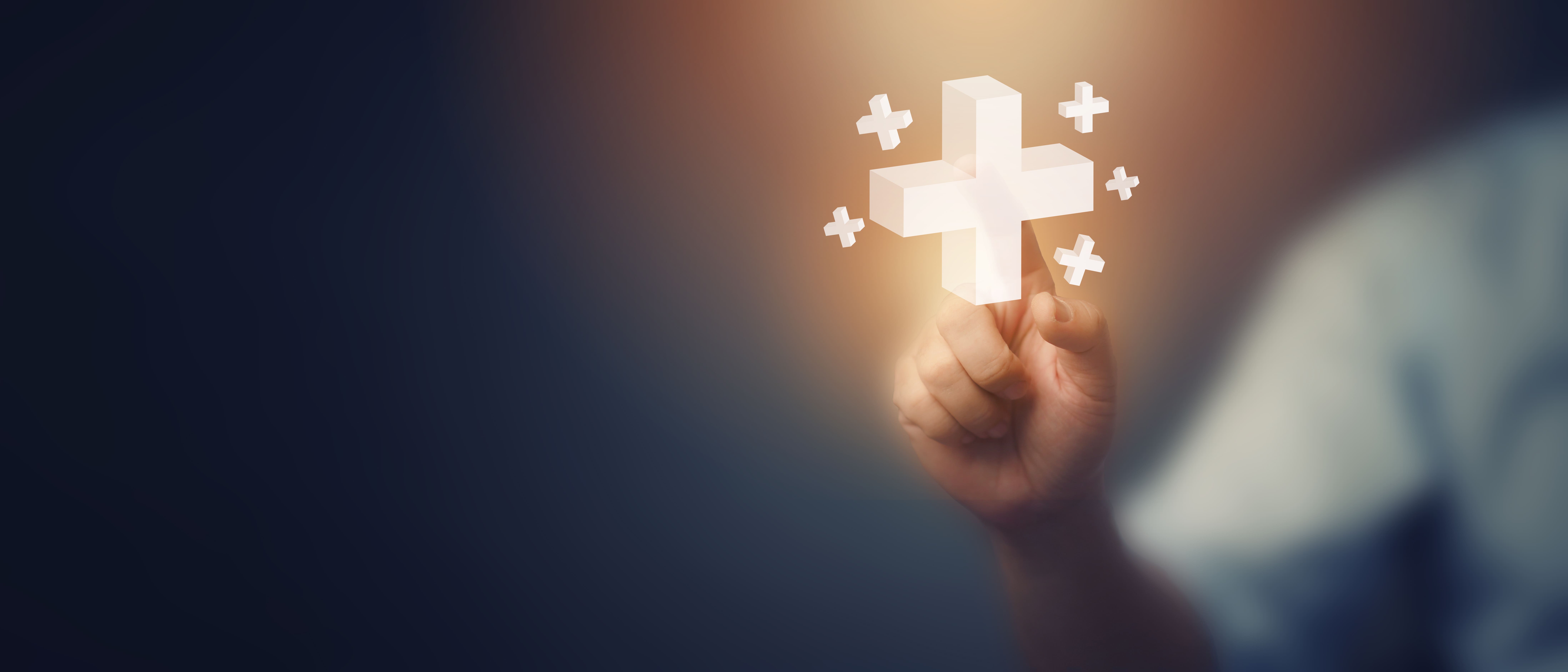
Top 10 Benefits of Progressive Web Apps (PWA)
- What is Warehouse Management?
- Essential Functions of Warehouse Management
- Crucial Warehouse Management System Features & Requirements
- Enhance Your Warehouse Management: Practical Tips
- How Inventorsoft Can Help You with Warehouse Management